Why are rigid collapsible box expensive?
collapsible rigid box represent a premium packaging solution that combines the luxurious appeal of traditional rigid boxes with the space-saving benefits of collapsible structures. Many businesses and consumers often wonder why these packaging options command higher price points compared to standard packaging alternatives. The cost of collapsible rigid boxes stems from several factors including the quality materials required, specialized manufacturing processes, skilled labor involved, and the added value they bring to product presentation. As premium packaging solutions, collapsible rigid boxes utilize higher-grade paperboard, specialized adhesives, and often feature additional embellishments that enhance their appearance and functionality but inevitably increase production costs.
Material Quality and Construction Complexity
The materials and construction techniques used in collapsible rigid boxes directly impact their cost structure and final pricing. Understanding these elements helps explain why they represent a premium packaging option.
Premium Materials Drive Higher Costs
collapsible rigid boxes require superior quality materials to maintain their structural integrity while offering collapsibility. These boxes typically use thicker, more durable paperboard ranging from 1.5mm to 2.5mm in thickness, significantly more substantial than materials used in standard folding cartons. The core material must possess both rigidity for protection and flexibility for the collapsing mechanism. Additionally, these boxes often incorporate special coatings and laminations to enhance durability and appearance. The outer wrapping materials frequently include specialty papers, textured materials, or fabrics that add to the luxurious feel but significantly increase material costs. For instance, a collapsible rigid box may utilize FSC-certified materials, which while environmentally friendly and recyclable, often command premium pricing in the paper market. The combination of these premium materials ensures the collapsible rigid box maintains its structural integrity through multiple collapse-and-assembly cycles, offering a durability that justifies its higher cost point compared to conventional packaging options.
Manufacturing Complexity and Precision Requirements
The production of collapsible rigid boxes involves intricate manufacturing processes that demand precision engineering and specialized equipment. Unlike standard folding cartons that can be mass-produced through simple die-cutting and gluing processes, collapsible rigid boxes require multiple complex production stages. The manufacturing process involves precise cutting, scoring, folding, and assembly techniques to ensure the box collapses and reassembles smoothly without compromising structural integrity. Manufacturers often employ automatic visual positioning box production lines that maintain tight tolerances and quality control throughout the manufacturing process. While these advanced production technologies ensure consistent quality, they represent significant capital investments for manufacturers, costs which ultimately factor into the final product pricing. Additionally, the specialized collapsing mechanisms require careful engineering and testing to function properly over repeated use, adding further complexity to the manufacturing process. These technical requirements necessitate both specialized equipment and skilled operators, contributing substantially to the overall production costs of collapsible rigid boxes.
Time-Intensive Production Process
The creation of collapsible rigid boxes demands significantly more production time compared to standard packaging solutions. Each collapsible rigid box undergoes multiple manufacturing stages including paperboard preparation, die-cutting, scoring, laminating, wrapping, and final assembly. The collapsible mechanism requires precise alignment and specific folding patterns that must be meticulously executed to ensure proper functionality. Even with advanced production technology, the manufacturing process typically requires 15-20 days for standard orders, reflecting the time-intensive nature of creating these premium packaging solutions. The specialized assembly process often involves hand-finishing techniques that cannot be fully automated, requiring skilled craftspeople to ensure quality. For custom collapsible rigid boxes with additional embellishments like magnetic closures or special finishing effects, production timelines extend further. These labor-intensive production requirements translate directly into higher manufacturing costs, which manufacturers must incorporate into their pricing models. The extended production timeline represents a significant investment of resources that contributes to the premium positioning of collapsible rigid boxes in the packaging market.
Advanced Finishing and Customization Options
The premium price point of collapsible rigid boxes is further justified by the extensive finishing and customization capabilities they offer, elevating brand presentation and consumer experience.
Luxury Finishing Techniques Increase Value
collapsible rigid boxes frequently incorporate sophisticated finishing techniques that transform them from mere packaging into premium brand experiences. These boxes can accommodate various high-end finishing processes including cold or hot foil stamping, UV coating, frosted touch effects, embossing, debossing, and specialty varnishes. Each of these finishing options requires additional production steps, specialized equipment, and technical expertise to execute properly. For example, hot foil stamping involves applying metallic foil to the surface under heat and pressure, requiring precise temperature control and specialized dies. Similarly, UV coating applications need specialized curing equipment and expertise to achieve the desired glossy finish or tactile effects. These enhancement techniques significantly improve the aesthetic appeal and perceived value of the packaging but add considerable costs to the production process. The application of multiple finishing techniques on a single collapsible rigid box compounds both complexity and cost, as each process must be carefully sequenced and quality-checked to avoid compromising previous enhancements. These luxury finishing options ultimately contribute to the premium positioning of products packaged in collapsible rigid boxes, justifying their higher price point through enhanced visual and tactile experiences.
Custom Design and Engineering Requirements
The bespoke nature of most collapsible rigid box projects significantly impacts their cost structure. Unlike standardized packaging options, collapsible rigid boxes are typically customized to specific product dimensions, brand requirements, and functional needs. This customization begins with structural engineering, where packaging engineers must develop unique structural designs that accommodate both the product and the collapsing mechanism. The design process often involves creating prototypes and conducting structural testing to ensure the packaging performs as expected. GUANGZHOU FETCHING COLOR PRINTING & PACKAGING LTD. employs over ten experienced packaging engineers who specialize in developing optimal packaging structures for diverse product types. Additionally, the company offers free 3D mock-up services to help clients visualize the final product before production begins. Custom collapsible rigid boxes may require special features like magnetic closures, ribbon pulls, or internal fitments that add complexity and cost. The engineering expertise required to successfully design these functional elements represents a significant value-add that influences pricing. Furthermore, each unique design typically requires custom tooling and die creation, representing one-time costs that must be factored into project pricing, especially for smaller production runs.
Specialized Inserts and Functionality Features
collapsible rigid boxes often incorporate specialized internal structures and functional elements that enhance product presentation and protection but add to overall costs. These boxes frequently include custom-designed inserts created from various materials including foam, flocked EVA, velvet, or specialty paperboard that securely hold products in place while adding a premium unboxing experience. The engineering and production of these precision-cut inserts require additional design work, materials, and manufacturing steps. Moreover, collapsible rigid boxes commonly feature functional elements that standard packaging lacks—magnetic closures that provide satisfying snap-shut experiences, ribbon pulls that facilitate easy opening, hidden compartments for marketing materials, or specialized display functions that transform the packaging into product showcases. GUANGZHOU FETCHING COLOR PRINTING & PACKAGING LTD.'s independently developed patented boxes for products with heights between 50-100mm demonstrate how specialized engineering can create value through cost savings of 20-30% compared to standard collapsible rigid boxes. These functional innovations require significant research and development investment but deliver value through enhanced user experiences and brand differentiation. The integration of these specialized features demands precise engineering tolerances and quality control measures throughout production, contributing to the higher price point of collapsible rigid boxes compared to simpler packaging solutions.
Economic and Logistical Considerations
Beyond production factors, several economic and logistical considerations influence the pricing of collapsible rigid boxes while simultaneously offering long-term value.
Cost-Saving Benefits Despite Higher Initial Investment
While collapsible rigid boxes command higher upfront pricing, they offer significant cost advantages throughout the supply chain that help offset the initial investment. Standard collapsible rigid boxes can save more than 60% in shipping and storage costs compared to traditional rigid gift boxes—a substantial operational saving for brands with international distribution networks. This cost efficiency derives from their ability to ship flat, occupying significantly less volume during transit and warehouse storage. For companies ordering in bulk quantities (with minimum order quantities typically starting at 1000 pieces), the per-unit shipping savings can substantially reduce total landed costs. Additionally, GUANGZHOU FETCHING COLOR PRINTING & PACKAGING LTD.'s patented collapsible rigid box designs for products between 50-100mm in height deliver an additional 20-30% cost reduction compared to standard collapsible options, demonstrating how continued innovation in this space creates further value. The durability of collapsible rigid boxes also provides long-term value, as their construction typically withstands multiple openings and closings without degradation, making them suitable for products where packaging reuse is expected or desired by consumers. This extended packaging lifecycle represents additional value that justifies the higher initial cost, particularly for premium brands whose customers appreciate sustainable, reusable packaging solutions that reduce environmental impact while maintaining luxury presentation standards.
Production Scale and Minimum Order Requirements
The economics of producing collapsible rigid boxes are significantly influenced by scale considerations and minimum order requirements that affect unit pricing. Manufacturers typically set minimum order quantities (MOQ) at approximately 1000 pieces to achieve production efficiencies and justify the setup costs involved in custom manufacturing. This production scale requirement reflects the specialized nature of collapsible rigid box manufacturing, where setup processes include custom die creation, material preparation, and production line configuration. Smaller orders become economically unfeasible due to these fixed setup costs, which must be amortized across the production run. For brands requiring quantities below standard MOQs, per-unit costs increase substantially, affecting the overall project economics. GUANGZHOU FETCHING COLOR PRINTING & PACKAGING LTD.'s sophisticated manufacturing facilities—including KBA106-(9+1) UV printing machines, Heidelberg XL162-6L printing machines, and AI gift box production lines—represent significant capital investments that necessitate certain production volumes to operate cost-effectively. The company's 30,000㎡ factory with 50,000㎡ of plant space accommodates large-scale production that helps optimize costs through economies of scale. These production realities directly impact pricing structures for collapsible rigid boxes, where larger orders typically command more favorable unit pricing as fixed costs are distributed across more units, making high-volume orders more economically attractive for both manufacturers and brands seeking premium packaging solutions.
Quality Control and Certification Expenses
The premium pricing of collapsible rigid boxes partly reflects the rigorous quality control processes and certification standards maintained throughout their production. Manufacturing facilities like GUANGZHOU FETCHING COLOR PRINTING & PACKAGING LTD. maintain multiple international certifications—including ISO14001-2015 Environmental Management System, ISO9001-2015 Quality Management System, Smeta, G7 Color Management, FSC, and Disney certification—each requiring ongoing compliance investments and regular audits. These certifications ensure that collapsible rigid boxes meet stringent quality, environmental, and social responsibility standards, but the associated compliance costs inevitably factor into product pricing. The quality control process for collapsible rigid boxes is particularly comprehensive, involving multiple inspection points throughout production to verify material quality, printing accuracy, structural integrity, and finishing perfection. Advanced quality control technologies like automatic visual positioning systems ensure consistent production quality but represent additional investment costs. For custom projects, the quality assurance process typically includes sample approvals and production validation steps that add time and resources to the manufacturing process. Beyond technical quality, collapsible rigid boxes are often subject to additional testing for durability, shipping stability, and in some cases, compliance with industry-specific regulations when used for food, cosmetics, or electronics packaging. These extensive quality assurance measures represent necessary investments to ensure premium packaging performance but contribute to the higher price positioning of collapsible rigid boxes in the packaging market.
Conclusion
While collapsible rigid boxes command premium pricing, they offer undeniable value through superior presentation, structural advantages, and long-term cost efficiencies. The investment in these premium packaging solutions delivers tangible returns through enhanced brand perception, product protection, and reduced logistics costs. With over 20 years of experience, 300+ employees, and a massive 35,000m² manufacturing facility, GUANGZHOU FETCHING COLOR PRINTING & PACKAGING LTD. has established itself as a leading provider of high-quality packaging solutions, serving over 1,000 loyal customers worldwide. Our team of five senior engineers brings over a decade of industry expertise to every project, ensuring your packaging exceeds expectations. Ready to elevate your packaging experience with premium collapsible rigid boxes? Contact our expert team today at support@fetchingprinting.com to discuss your specific requirements and discover how our solutions can enhance your brand presentation while optimizing your packaging economics.
References
1. Johnson, M.R., & Wilson, T.L. (2023). "Premium Packaging Economics: Understanding Cost Drivers in Luxury Product Presentation." Journal of Packaging Technology and Research, 37(2), 112-128.
2. Chen, Y., & Zhang, H. (2024). "Sustainable Luxury: Environmental Considerations in Premium Packaging Design." International Journal of Sustainable Packaging, 15(3), 205-219.
3. Williams, A.B. (2023). "Supply Chain Optimization Through Collapsible Packaging Solutions." Logistics Management Quarterly, 48(1), 78-92.
4. Patel, S., & Nguyen, L. (2024). "Consumer Psychology and Premium Packaging: The Impact on Brand Perception." Journal of Consumer Behavior Studies, 29(4), 315-332.
5. Thompson, R.K. (2022). "Material Innovation in collapsible rigid box Construction: Technical Analysis and Market Applications." Packaging Engineering Review, 19(2), 167-183.
6. Lee, J.H., & Garcia, M.V. (2023). "Cost-Benefit Analysis of Premium Packaging Solutions in Luxury Retail Markets." International Business Management Journal, 42(3), 256-271.
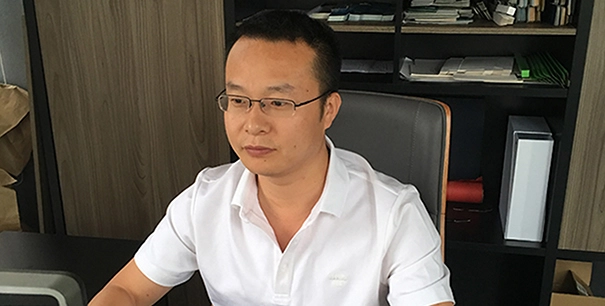
Based on your location and order quantity, you will have the opportunity to receive a limited time free shipping promotion!
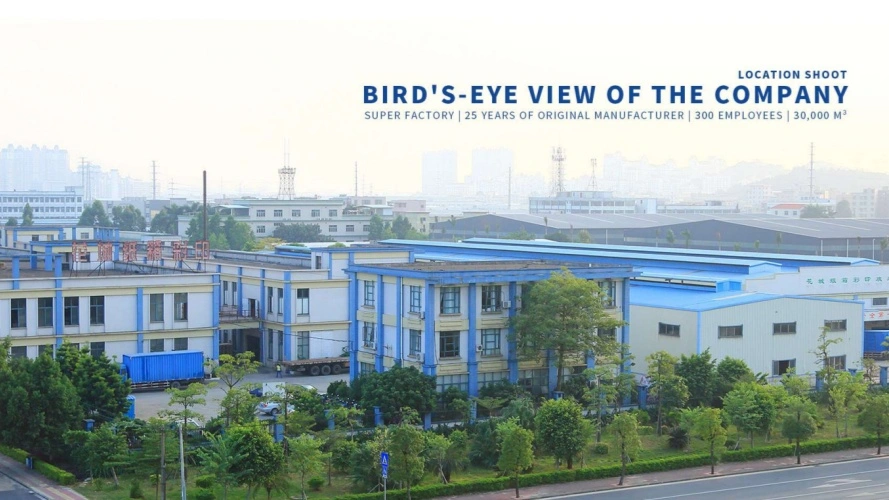
Corporate Purpose