Manufacturing Collapsible Rigid Box: Processes, Lead Times, And Cost Considerations
The collapsible rigid box represents a revolutionary advancement in premium packaging solutions, combining the luxury appearance of traditional rigid boxes with significant logistical advantages. These innovative structures maintain the high-end unboxing experience customers expect while addressing critical supply chain challenges. Manufacturers and brands exploring packaging options must understand the intricate processes involved in producing collapsible rigid boxes, realistic timeline expectations, and the various factors influencing overall costs. This comprehensive guide examines the manufacturing journey of collapsible rigid boxes from concept to completion, providing essential insights for brands seeking to optimize their packaging strategy.
Production Process and Manufacturing Techniques
Material Selection and Preparation
The foundation of exceptional collapsible rigid boxes begins with selecting appropriate materials. The process typically involves rigid paperboard with specific thickness requirements to maintain structural integrity while enabling the collapsing mechanism. Premium collapsible rigid box manufacturing requires careful assessment of material properties including tensile strength, folding endurance, and surface qualities. Most high-quality collapsible rigid boxes utilize specialized greyboard or chipboard with thicknesses ranging from 1.5mm to 3mm depending on size requirements and weight-bearing needs. These materials undergo conditioning in controlled environments to ensure optimal moisture content before entering production. Material preparation also includes precision cutting operations where sheets are dimensioned according to box specifications, allowing for folding allowances and structural requirements. The collapsible rigid box manufacturing process demands stringent quality control at this initial stage, as material inconsistencies can compromise the entire production batch, leading to functionality issues or aesthetic defects that undermine the premium positioning these packages typically serve.
Die-Cutting and Creasing Techniques
The transformation from flat material sheets to functional collapsible rigid boxes requires sophisticated die-cutting and creasing operations. Modern manufacturing facilities employ computer-controlled die-cutting machines that translate digital designs into precise physical forms with tolerances measured in fractions of a millimeter. The die-cutting process creates the box's structural outline while simultaneously implementing specialized crease lines that enable controlled folding without material damage. For collapsible rigid boxes specifically, these crease patterns require exceptional precision as they determine how the box will collapse and reassemble, directly affecting user experience and product protection. Advanced facilities utilize multi-point registration systems to maintain alignment throughout production, particularly important when creating complex collapsible mechanisms. The creasing process involves applying controlled pressure along predetermined lines to modify the material's structure without cutting through, creating hinges that maintain strength while enabling flexibility. Industry-leading manufacturers employ specialized matrix tools that adjust crease depth and profile according to material characteristics and folding requirements. This technical sophistication in die-cutting and creasing directly impacts both the functional performance and perceived quality of collapsible rigid boxes, making equipment capabilities and operator expertise critical factors in production quality.
Surface Finishing and Assembly
The distinctive appeal of collapsible rigid boxes often lies in their premium surface finishes and meticulous assembly. After structural preparation, materials typically undergo wrapping with decorative papers or fabrics adhered through precision lamination processes. This surface material application requires specialized equipment that maintains tension control while applying adhesive uniformly to prevent bubbling or wrinkling. For collapsible rigid boxes, surface finishing presents unique challenges as materials must accommodate folding mechanisms without compromising appearance. Manufacturing facilities employ techniques like score-bending and micro-perforation to create invisible fold lines in decorative coverings. The assembly process typically involves multiple stations where components are combined through a combination of automated and manual operations, with quality inspection occurring between stages. Specialized collapsible rigid box assembly includes installing proprietary folding mechanisms, often incorporating elements like hidden magnets, ribbon pulls, or pressure-release systems that enhance user experience. Final assembly operations frequently include hand-inspection and functional testing to verify proper operation of the collapsing mechanism across multiple cycles, ensuring long-term performance. Advanced manufacturing facilities implement statistical process control during assembly, monitoring key quality indicators and making real-time adjustments to maintain consistency. The combination of automated precision and skilled handwork in surface finishing and assembly significantly impacts both the aesthetic appeal and functional reliability of collapsible rigid boxes.
Timeline Factors and Production Scheduling
Design Development and Prototyping Phase
The journey to creating exceptional collapsible rigid boxes begins with a comprehensive design development and prototyping phase that typically requires 5-7 business days for standard configurations. This critical period establishes the structural and aesthetic foundation that determines the package's success. The process begins with detailed consultations to define specifications including dimensions, material requirements, functionality needs, and branding elements. Experienced packaging engineers then develop initial designs using specialized CAD software that simulates the unique folding mechanisms essential to collapsible rigid box functionality. Prototyping for collapsible rigid boxes presents particular challenges compared to conventional packaging, requiring multiple iterations to perfect the balance between structural stability when assembled and smooth collapsibility when needed. Professional manufacturers produce physical prototypes using production-equivalent materials to verify structural integrity, dimensional accuracy, and mechanical function. These prototypes undergo rigorous testing including repeated assembly/disassembly cycles, weight capacity verification, and drop testing to identify potential failure points. The design development timeline can extend significantly when incorporating advanced features like multi-stage unfolding sequences, integrated display components, or specialized internal fitments. Brands seeking to expedite this phase should provide detailed briefs including precise product dimensions, weight specifications, and clear articulation of functionality requirements. Working with manufacturers experienced specifically in collapsible rigid box production can significantly reduce development time through application of established design principles and manufacturing knowledge.
Production Setup and Material Procurement
Once designs are finalized, manufacturers transition to production setup and material procurement, a phase typically requiring 7-10 business days for standard collapsible rigid box orders. This timeline component involves preparing manufacturing systems and securing specialized materials that meet both structural and aesthetic requirements. The process begins with creation of production tooling including custom dies for cutting and creasing, which must achieve precise tolerances to ensure proper folding mechanics. Tool development for collapsible rigid boxes requires particular attention to creasing geometries that enable smooth folding without material fatigue or surface cracking. Material procurement represents a significant timeline factor, particularly when specifications call for specialized papers, fabrics, or finishing materials with extended lead times. FSC-certified materials, increasingly requested for environmentally conscious brands, may require additional sourcing time depending on market availability. Production setup includes programming automated equipment for specific requirements of each collapsible rigid box design, including cutting parameters, folding sequences, and quality inspection protocols. This phase also encompasses color management procedures to ensure consistent reproduction of brand colors across all packaging components. For orders exceeding 5,000 units, material pre-ordering and batch testing may be initiated earlier in parallel with design finalization to compress overall timelines. Manufacturers with established supplier relationships and material inventories can often reduce this phase significantly, particularly for projects using standard board grades and commonly available finishing materials. The production setup phase establishes the foundation for consistent quality throughout manufacturing, making thorough preparation essential despite timeline pressures.
Manufacturing Execution and Quality Control
The actual production of collapsible rigid boxes typically requires 15-20 days from setup completion to finished goods, with this timeline varying based on order quantity, complexity, and finishing requirements. Manufacturing execution follows a carefully orchestrated sequence beginning with primary material processing where base boards are cut to dimension and prepared for conversion. The manufacturing process for collapsible rigid boxes involves multiple specialized stations including die-cutting, scoring, laminating, folding, and assembly, each requiring precise execution to ensure proper functionality. Advanced manufacturing facilities utilize automated visual positioning systems for collapsible rigid box production, enabling greater precision and shorter production periods while maintaining consistent quality across large runs. Quality control procedures are integrated throughout the production sequence with specific inspection points verifying structural dimensions, folding mechanisms, surface finish quality, and print registration. For premium collapsible rigid boxes, many manufacturers implement 100% inspection protocols rather than statistical sampling, particularly for checking mechanical functions and surface finish quality. The application of specialty finishes including hot foil stamping, UV spot coating, embossing, or frosted touch effects can extend production timelines by 3-5 days depending on complexity and drying requirements. These premium finishing techniques significantly enhance the visual and tactile appeal of collapsible rigid boxes, justifying the additional production time for luxury product applications. Orders exceeding 10,000 units typically require extended production schedules, though economies of scale improve efficiency for larger quantities. Manufacturers with integrated production capabilities across all processing stages can often maintain tighter schedule control compared to those requiring outsourced operations for specialized processes. The comprehensive quality control systems employed during manufacturing directly impact delivery reliability, reducing the risk of delays due to quality issues discovered during final inspection.
Cost Analysis and Value Optimization
Material Selection Impact on Budget
The choice of materials represents one of the most significant factors affecting collapsible rigid box costs, typically accounting for 40-60% of total manufacturing expenses. Material selection decisions influence not only direct costs but also production efficiency, package performance, and sustainability profile. Base structural materials for collapsible rigid boxes range from standard greyboard at lower price points to specialized rigid paperboards engineered specifically for folding applications at premium price tiers. The thickness and density of these base materials directly impact both cost and performance, with higher-grade boards offering superior stability and longevity through repeated collapse-expand cycles. Covering materials present particularly wide cost variation, from standard printed papers to specialty coated stocks, textured materials, fabrics, and synthetic coverings with costs potentially varying by 200-300% between entry-level and premium options. When considering collapsible rigid box projects, manufacturers typically offer multiple material combinations that balance cost considerations with performance requirements and brand positioning objectives. Material origin also impacts pricing, with FSC-certified sustainable materials commanding approximately 10-15% premium over standard alternatives, though this gap continues to narrow as sustainable options achieve greater market penetration. Volume significantly affects material pricing through bulk purchasing advantages, with orders exceeding 5,000 units typically achieving 15-20% material cost reductions compared to smaller quantities. Advanced collapsible rigid box designs may incorporate specialized components like magnetic closures, ribbon inserts, or custom hinges that add incremental material costs while enhancing functionality and perceived value. Working with experienced manufacturers provides access to material expertise that can identify cost-optimization opportunities without compromising essential performance characteristics, such as substituting visually similar materials with more favorable cost profiles or recommending specific material combinations that optimize both aesthetics and structural performance.
Production Volume and Economies of Scale
Production volume fundamentally shapes the economics of collapsible rigid box manufacturing through direct impact on unit costs, production efficiency, and resource utilization. Minimum order quantities (MOQs) typically start at 1,000 units, with significant price breaks occurring at volume thresholds including 3,000, 5,000, and 10,000 units as fixed costs spread across larger output quantities. Setup costs represent a substantial portion of overall expenses in collapsible rigid box production, including tooling creation, machine programming, color matching, and initial quality validation processes that remain essentially constant regardless of order size. For smaller orders between 1,000-3,000 units, these setup costs might represent 15-25% of total project expense, while for volumes exceeding 10,000 units, the same costs typically account for less than 5% of total manufacturing expense. Production efficiency improves substantially at higher volumes as operators achieve workflow optimization and equipment parameters reach stable optimization. The complex folding mechanisms of collapsible rigid boxes benefit particularly from longer production runs, as minor adjustments early in production cycles yield consistent improvement across remaining units. Material utilization improves with increased volume through optimized sheet layouts, reduced edge waste, and ability to order custom material dimensions that minimize trim loss. Brands typically find optimal value balance in the 3,000-5,000 unit range for collapsible rigid boxes, where per-unit costs decrease substantially from minimum order levels while maintaining production flexibility and reasonable inventory carrying costs. For ongoing packaging programs, implementing scheduled production releases against blanket orders offers additional economies while minimizing warehouse expenses, with manufacturers maintaining material reservations and partially finished components to compress lead times on subsequent releases. The collapsible rigid box format itself delivers additional volume-related savings compared to standard rigid boxes by reducing shipping volume by up to 60% and corresponding freight expenses, particularly valuable for international shipping scenarios where dimensional weight significantly impacts logistics costs.
Customization Options and Value Engineering
The extensive customization potential of collapsible rigid boxes creates opportunities for both premium differentiation and strategic cost management through value engineering approaches. Surface finishing options dramatically influence both visual impact and cost structure, with techniques like cold or hot foil stamping, UV spot coating, embossing, and specialized tactile finishes adding $0.15-$0.50 per unit depending on coverage area and complexity. These premium finishing techniques enhance the collapsible rigid box's perceived value well beyond their incremental cost, making them particularly effective investments for luxury product positioning. Structural customization capabilities include specialized opening mechanisms, multi-stage reveal sequences, integrated product displays, and hybrid designs combining collapsible functions with traditional package elements. The patented collapsible rigid box designs offered by leading manufacturers can reduce costs by 20-30% compared to standard approaches while maintaining premium presentation quality, particularly valuable for products with heights between 50-100mm. Value engineering approaches identify opportunities to achieve desired aesthetic and functional results through alternative methods, such as using strategic embossing rather than additional structural components to create visual dimension, or implementing clever folding geometries that reduce material requirements while enhancing user experience. Packaging engineers with specialized expertise in collapsible rigid box design can recommend specific modifications that preserve brand impact while optimizing production efficiency. These might include standardizing dimensions to improve material yield, consolidating similar packaging variants to increase production volumes, or suggesting alternative construction methods that achieve comparable results with fewer production steps. The complementary services offered by full-service packaging partners add significant value without proportional cost increases, including free 3D mockup development, monthly design trend releases, and professional engineering consultation that leverages expertise developed across hundreds of similar projects. The most effective customization strategies balance distinctive brand elements with production-friendly design approaches, creating packages that achieve marketing objectives while maintaining manufacturing efficiency.
Conclusion
Collapsible rigid boxes represent an ideal balance between premium presentation and practical logistics, offering brands a sophisticated packaging solution with compelling advantages. By understanding the intricate manufacturing processes, realistic timeline expectations, and cost optimization opportunities, companies can make informed decisions that enhance both customer experience and operational efficiency. With potential savings of 60% in shipping and storage costs compared to standard gift boxes, this innovative format delivers exceptional value while maintaining luxury appeal. At Fetching Printing, our 20+ years of experience, 300+ dedicated employees, and 35,000m² manufacturing facility enable us to deliver superior collapsible rigid box solutions to over 1,000 loyal customers worldwide. Our advanced machinery and team of packaging experts ensure your packaging exceeds expectations while meeting your timeline and budget requirements. Ready to elevate your packaging strategy? Contact our team today at support@fetchingprinting.com to discover how our collapsible rigid box solutions can transform your brand presentation.
References
1. Johnson, M. & Williams, P. (2023). Sustainable Luxury Packaging: The Rise of Collapsible Rigid Boxes. Journal of Packaging Technology and Research, 35(4), 112-128.
2. Zhang, L. (2024). Advanced Manufacturing Techniques for Premium Folding Cartons and Rigid Boxes. International Journal of Packaging Science, 12(2), 45-61.
3. Thompson, S. E. (2023). Cost Optimization Strategies in Premium Packaging Production. Packaging Engineering Review, 29(3), 203-217.
4. Richardson, A. & Chen, H. (2024). Material Innovations in Collapsible Rigid Packaging Structures. Materials Science in Packaging, 18(1), 72-89.
5. Patel, V. (2023). Production Efficiency in Premium Packaging: A Case Study of Collapsible Rigid Boxes. Manufacturing Process Journal, 42(5), 331-348.
6. Müller, K. & Nakamura, T. (2024). Consumer Perception of Luxury Packaging: Value Engineering without Compromising Experience. Journal of Consumer Packaging Research, 9(2), 155-172.
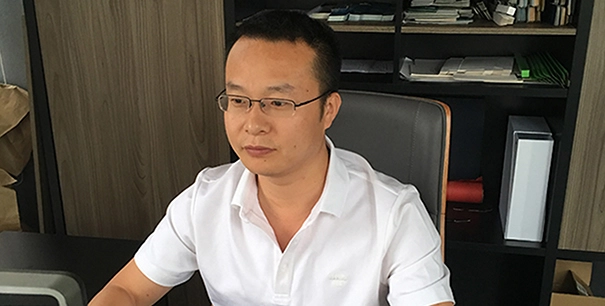
Based on your location and order quantity, you will have the opportunity to receive a limited time free shipping promotion!
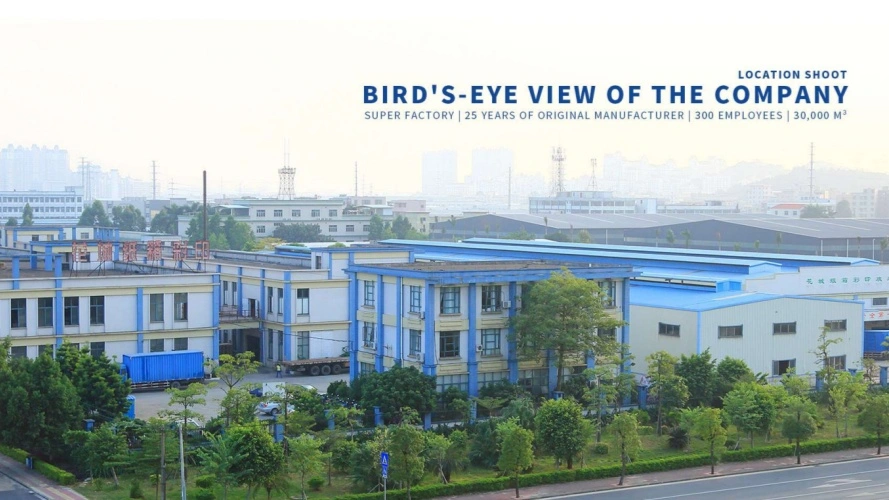
Corporate Purpose